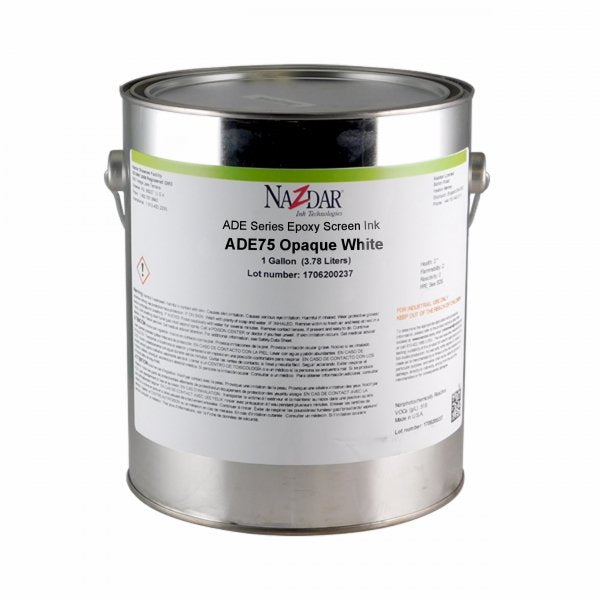
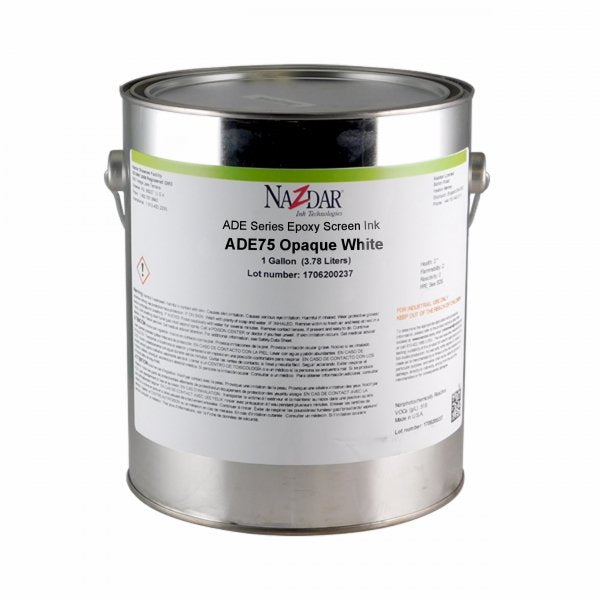
ADE Series epoxy solvent-based screen ink has been formulated with high quality epoxy resins
for excellent adhesion to metals, glass and a wide range of hard-to-print substrates. ADE Series is
ideal for electronic and industrial applications and provides outstanding solvent, chemical and
abrasion resistance. ADE is a two-part ink and must be initiated with a catalyst prior to use. ADE
ink exhibits a high gloss finish. ADE Series is for indoor applications only.
Substrates
- Metals
- Glass
- PC boards
- Epoxy
- Melamine
- Treated polyethylene
- Treated polypropylene
Substrate recommendations are based on commonly available materials intended for the ink’s specific
market when the inks are processed according to this technical data. While technical information and
advice on the use of this product is provided in good faith, the User bears sole responsibility for selecting
the appropriate product for their end-use requirements. Reference the ‘Quality Statement’ at the end of
this document.
User Information
Mesh 200-305 tpi (78-120 tpcm) monofilament polyester mesh or stainless steel mesh for most applications.
Stencil
Use direct emulsions and capillary films which are solvent resistant.
Squeegee
70-80 durometer polyurethane squeegee.
Coverage
Estimated 1,200-1,800 square feet (111-167 square meters) per gallon depending upon ink
deposit. Reference www.nazdar.com for examples of coverage calculations.
Printing
Ink Preparation: ADE Screen Ink is a two-part ink and must be initiated with a catalyst prior to use.
Various catalysts can be used; see the ‘Additives’ section. The amount of catalyst should only be
based on the weight of the ink and not include the weight of any other additives. Catalyzed ink
requires an “induction period” or time lag of about 30 to 45 minutes to allow the catalyst to
become uniformly mixed and available for the polymerization (cross linking) process.
Add only enough ink to the screen to be able to print for 5-10 minutes. Add additional ink in small
increments throughout the print run to maintain screen stability. Thoroughly mix the ink prior to
printing. Improper mixing can lead to inconsistent color and ink performance.
Maintain ink temperature at 65°-90°F (18°-32°C) for optimum print and cure performance. Lower
temperatures increase the ink viscosity, impairing flow and increasing film thickness. Elevated
temperatures lower the ink viscosity, reducing print definition and film thickness.
Pretest to determine optimum printing parameters for a particular set of ink, substrate,
screen, press, and curing variables/conditions.
Nazdar does not recommend inter-mixing of ADE Series with other inks besides the ADE Series.
Drying / Curing Parameters
ADE inks crosslink or cure over time as the residual solvent is evaporated from the printed
ink film. ADE inks dry to the touch before the ink film achieves full cure to exhibit required
adhesion, chemical resistance and surface hardness. At lower temperatures, drying and
curing takes place over longer periods of time; whereas elevated temperatures speed up the
process. At any temperature, it is necessary to maintain good air circulation to remove the
vaporized solvents. Residual solvents in the air inhibit the drying/curing process. Multiple layers
of ink may require longer drying times than a single layer.
The following are starting point guidelines to determine temperature and times to achieve a
crosslinked ink film.
Room Temperature: ADE Series dries to touch in approximately 30-60 minutes and cures in 5-7
days.